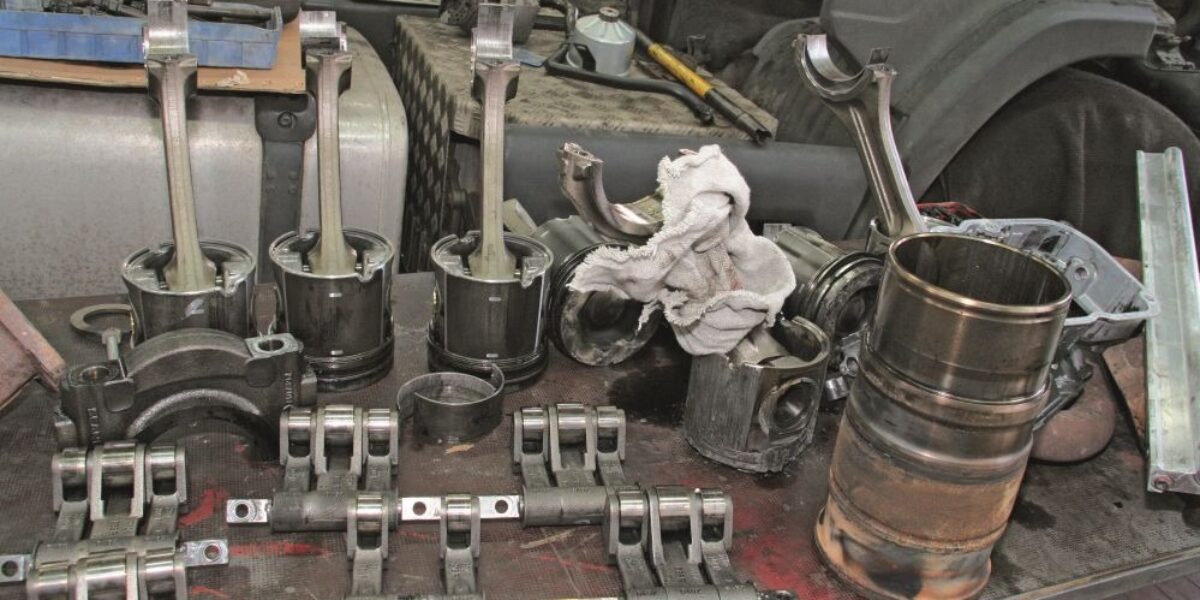
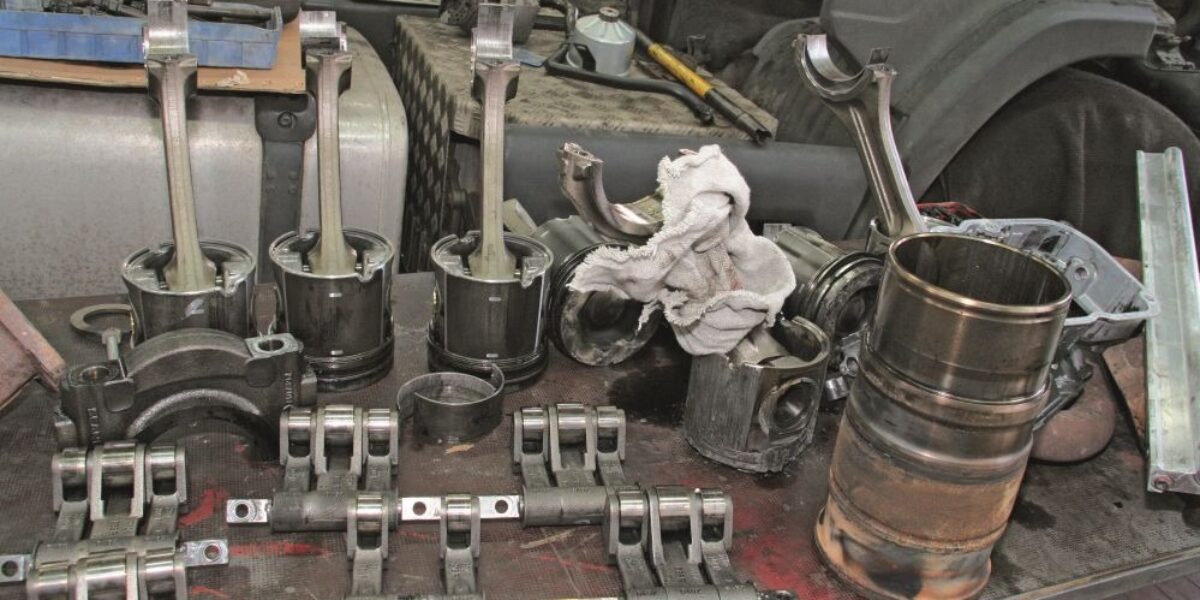
Welche Motorschäden sich mit Werkstattmitteln reparieren lassen
Mit jeder neuen Schadstoffnorm ist die Technik von Nutzfahrzeugmotoren komplexer geworden. Damit haben sich auch die Reparaturmethoden bei Defekten am Motor und seinen Komponenten verändert. Manche bislang, eher banale Schäden lassen sich deshalb mit Werkstattmitteln kaum noch fachgerecht reparieren beziehungsweise erfordern vom Werkstattfachmann spezielles Know-how sowie spezielles Equipment. Bei manchen Schadensbildern ist es vernünftig, einen professionellen Motoreninstandsetzer einzubinden. Dies ist besonders dann zu empfehlen, wenn es um eine knifflige Reparatur geht oder die Instandsetzung schadensbezogen und zeitwertgerecht durchgeführt werden soll.
Erschwerte Bedingungen
Mal eben die Zylinderkopfdichtung ersetzen, den Zylinderkopf planen und überholen, neue Zylinderlaufbuchsen und Kolben einbauen, oder die Kurbelwelle lagern – noch bis vor wenigen Jahren gehörten solche Arbeiten zum Tagesgeschäft in vielen Nfz-Werkstätten und zum Repertoire ‚gewöhnlicher‘ Nutzfahrzeugprofis. Doch mit der rasanten Entwicklung des Motorenbaus hat sich mindestens ebenso rasant das Thema Motoreninstandsetzung verändert.
Was leider nicht in gleichem Maße Schritt gehalten hat, ist vielfach das notwendige Know-how in klassischen Nfz-Werkstattbetrieben zum Thema Motoren. Insbesondere freie beziehungsweise markenfremde Werkstattbetreiber mussten vereinzelt schon bitteres Lehrgeld bezahlen. Sie haben sich ohne das erforderliche Hintergrundwissen oder mit fehlenden oder unvollständigen Reparaturinformationen an Instandsetzungsarbeiten herangewagt. Frei nach dem Motto „Das haben wir immer schon so gemacht!“ Letztendlich kam es zu teuren Folgereparaturen und schließlich zu Streitigkeiten mit dem Fahrzeugbesitzer.
Ganzheitlich diagnostizieren
Bei der Diagnose von Motordefekten wird es zunehmend wichtiger ‚ganzheitlich‘ zu denken. Denn neben klassischen, mechanischen und überwiegend laufzeit- oder wartungsbedingten Defekten wie Ventil-, Zylinderkopf-, Lager- und Kurbelwellenschäden haben es Werkstattfachleute zunehmend mit den negativen Auswirkungen moderner, mängelbehafteter Nebensysteme wie der Hochdruck-Dieseleinspritzung zu tun. Daher ist es heutzutage oft nicht mehr damit getan, die defekte Motorenkomponente, etwa den durchgebrannten Kolben, zu ersetzen, ohne nach der eigentlichen Schadensursache zu suchen. Beispiele sind verschlissene oder defekte Common-Rail-Injektoren.
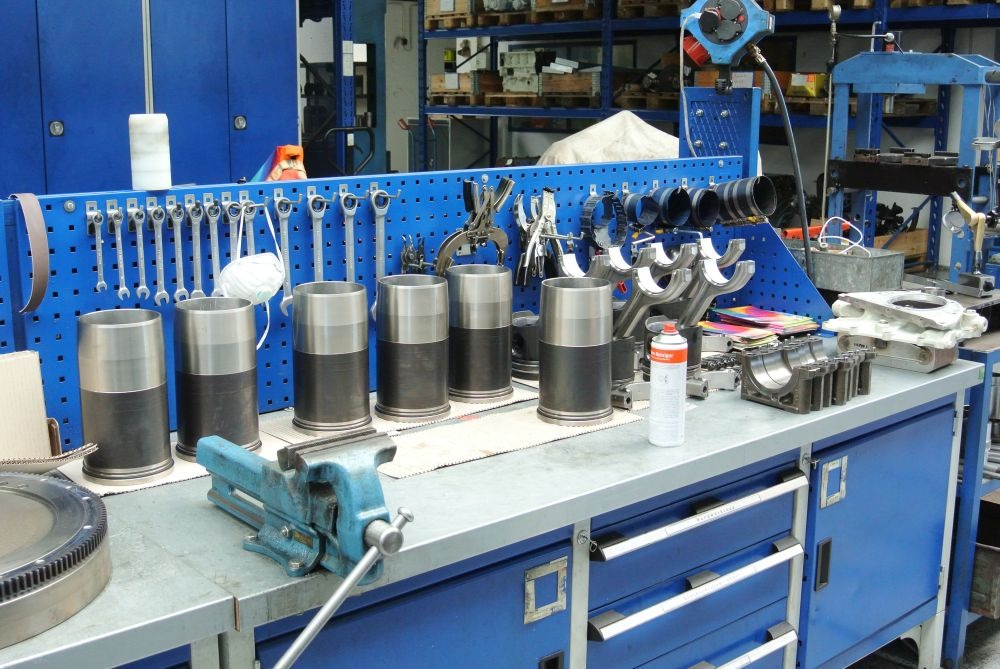
Je nach Motorenbauart und Schadensbild lassen sich Motorenreparaturen durchaus in ‚normalen‘ Nutzfahrzeug Werkstätten noch in Eigenregie und mit Werkstattmitteln erledigen. Allerdings sollte man die Herstellerliteratur beachten. Bild: Klaus Kuss
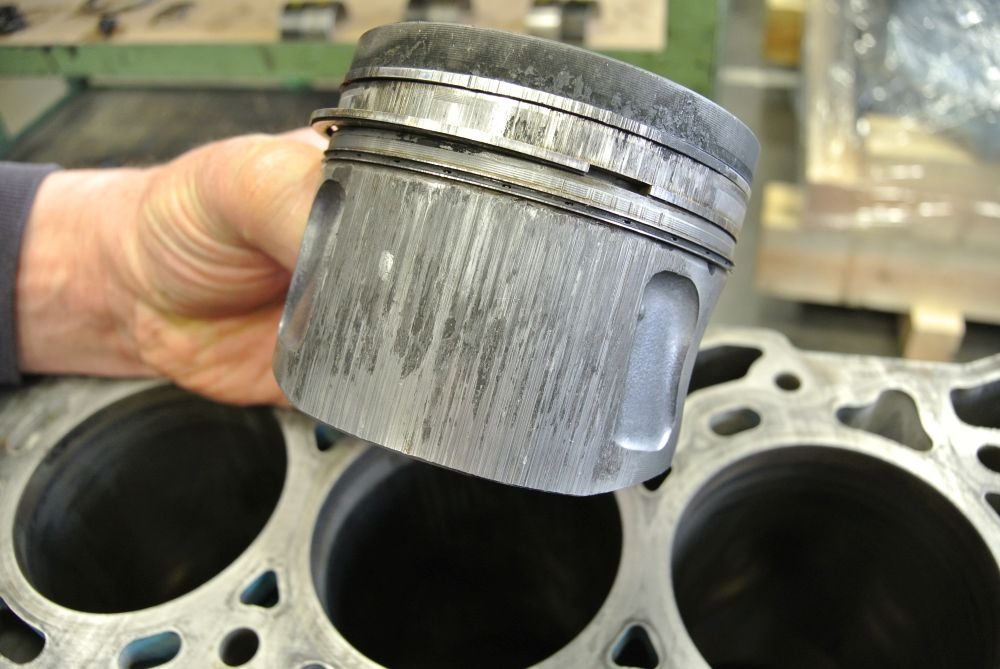
Bei der Diagnose von Motorschäden heißt es zunehmend ‚ganzheitlich denken‘, denn viele Schäden an der Motormechanik werden durch schadhafte Nebensysteme verursacht: Ist etwa ein CR-Injektor undicht oder tropft er permanent nach, wäscht es den Schmierfilm von der Zylinderwand und der Kolben frisst. Bild: Klaus Kuss
Wer die Peripherie nicht berücksichtigt riskiert teure Folgeschäden, die meist schon kurz nach der Reparatur auftreten, oder einen erneuten Motordefekt nach sich ziehen. Zugegeben: Bei nicht mehr lauffähigen Motoren ist eine umfassende Diagnose keine leichte Übung, doch das Schadensbild verrät einem erfahrenen Motorenprofi üblicherweise viel zur Vorgeschichte. Deshalb kann es im Zweifel vernünftig sein, einen professionellen Motoreninstandsetzer hinzuzuziehen.
Knackpunkt Dichtflächen
u den Standardaufgaben in der Nutzfahrzeug-Werkstatt gehört der Austausch der Zylinderkopfdichtung (ZKD). Eine Arbeit, die auf den ersten Blick kein Problem darstellen sollte. Doch mit dem Einzug von Metall-Elastomer-Zylinderkopfdichtungen bei Nutzfahrzeugmotoren sind die Anforderungen an die Oberflächengüte der Dichtflächen an Zylinderkopf und Motorblock enorm gestiegen. Während ‚antiquierte‘ Weichstoffdichtungen noch geringe Kratzer oder Vertiefungen in den Dichtflächen von Kopf und Block tolerierten, ist dies bei der modernen Dichttechnik nicht mehr der Fall. Sie verlangt eine genau definierte Oberflächenqualität, die sich mit Werkstattmitteln wie dem bewährten Schwingschleifer kaum gewährleisten lässt.
Prinzipiell gilt: je besser die Oberflächen, desto besser die Dichtwirkung. Doch eine zu glatte Bauteiloberfläche kann ebenfalls zu Undichtigkeiten führen, warnen die Spezialisten von Victor Reinz. Demnach bietet eine extrem glatte Oberfläche keine Angriffs- beziehungsweise Haltepunkte für die Elastomerbeschichtung der Metall-ZKD. Eine ordnungsgemäße Mikroabdichtung ist nicht gewährleistet. Den Experten zufolge liegt die optimale Oberflä chenrauigkeit von Zylinderkopf- beziehungsweise Motorblock-Dichtflächen zwischen sieben und 20 Mikrometern (µm), wobei die Welligkeit 20 µm nicht überschreiten sollte. Ähnlich hohe Maßstäbe gelten auch für Unebenheiten und Verzug an den Bauteilen: die gemessenen Werte sollten in Längsrichtung auf einer Länge von 100 Millimeter (mm) unter 0,03 mm, auf einer Länge von 1.000 mm unter 0,10 mm sowie in Querrichtung auf einer Länge von 100 mm unter 0,03 mm liegen. Die Welligkeit der Dichtfläche darf maximal 10 µm bei einem Abstand von > 8 mm betragen. Auch die Rauigkeiten bewegen sich mit Rz < 15 µm und Rmax < 20 µm in engen Grenzen. Derartig hohe Anforderungen lassen sich nur mit Spezialmaschinen, wie sie bei Motoreninstandsetzern zu finden sind, erreichen.
Bis zu einem gewissen Grad passen sich Metall-Elastomer-ZKD zwar an die Oberflächenbeschaffenheit an. Doch weichen die Werte von den vorab beschriebenen Vorgaben ab, oder verzichtet der Werkstattfachmann auf eine professionelle Nacharbeit, ist eine spätere Reklamation vorprogrammiert. Kratzer, Unebenheiten, Eingrabungen oder Verzug sind deshalb ein Fall für den Motoreninstandsetzer.
Spezielle Lösungen
Motor-Profis haben auch einige interessante Speziallösungen parat, mit denen sich knifflige Problemfälle fachgerecht in den Griff bekommen lassen. Etwa, wenn bei Stirnrad-getriebenen Lkw-Motoren die Dichtfläche am Zylinderkopf und/oder dem Motorblock nachbearbeitet und dabei vergleichsweise viel Material abgenommen werden musste. In einem solchen Fall lässt sich das abgetragene Material durch eine spezielle, entsprechend dickere Reparaturstufen-ZKD ausgleichen. Mit der Standarddichtung würden die Zahnflanken der Stirnräder zwangsweise zu stark ineinandergreifen, was zu einem schnellen Flankenverschleiß und kapitalen Motorschäden führen würde. Bei dieser Gelegenheit kann der Motorenprofi beispielsweise den Überstand von Einspritzdüsen und Kolben kontrollieren.
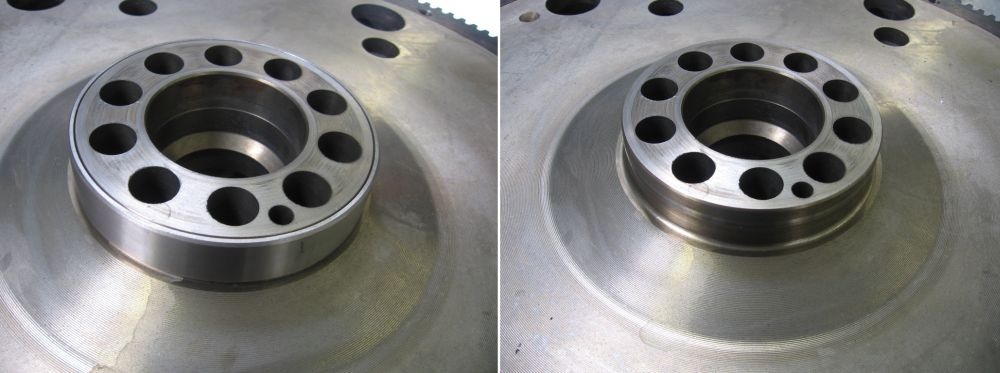
Eine weitere Spezialität der Instandsetzer ist die Reparatur von Ölundichtigkeiten an Kurbel-, Nocken-, Antriebs- und Nebenantriebswellen. Ist beispielweise die Dichtfläche an der Kurbelwelle oder dem Schwungrad eingelaufen, lässt sich mit dem Einbau einer speziellen Wellenschutzhülse ein kostspieliger Wellenersatz verhindern. Der Einbau der Hülse gestaltet sich simpel: Dichtfläche gründlich reinigen, Zustand der Dichtfläche beurteilen, grobe Verschleißspuren (Kerben, Riefen, Rauheiten) mit einer geeigneten Füllmasse egalisieren und die Wellenschutzhülse mit der Montagehilfe, die üblicherweise zum Lieferumfang gehört, anbringen. Zum Schluss noch den Montageflansch der Hülse abtrennen – fertig. Nach der Arbeit lässt sich ein Radialwellendichtring mit den ursprünglichen Abmessungen einbauen. Wellenschutzhülsen sind bei Anbietern wie MS Motorservice und SKF für Wellendurchmessern von zwölf bis 200 Millimeter erhältlich, weitere Größen gibt es meist auf Anfrage.
Den Beitrag finden Sie auch in der Print-Ausgabe 3/21 der Krafthand-Truck.