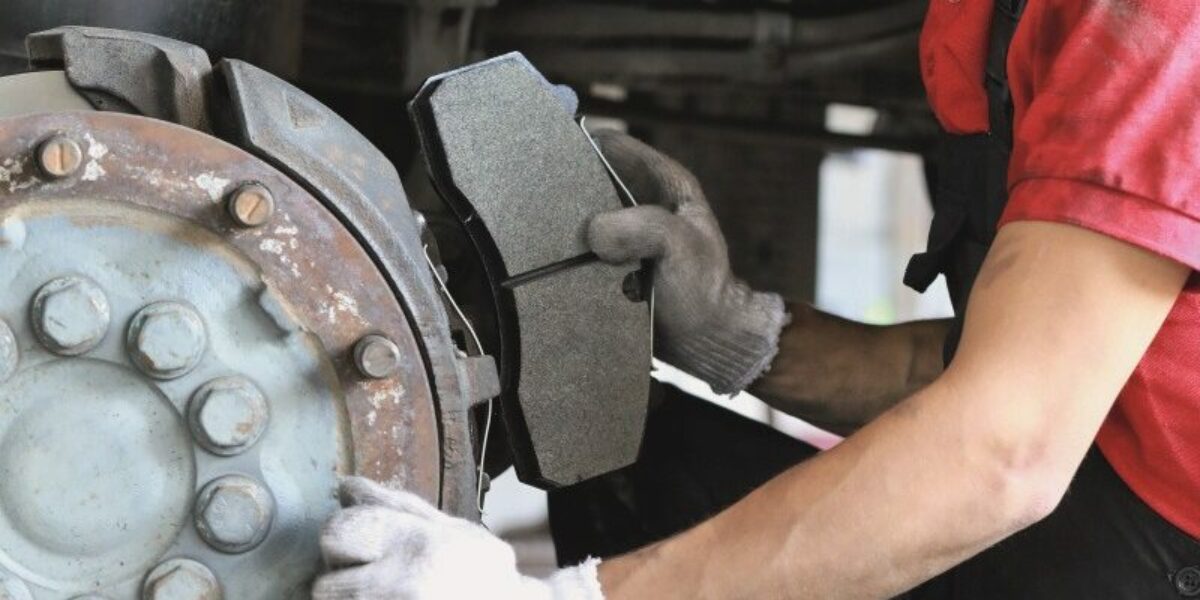
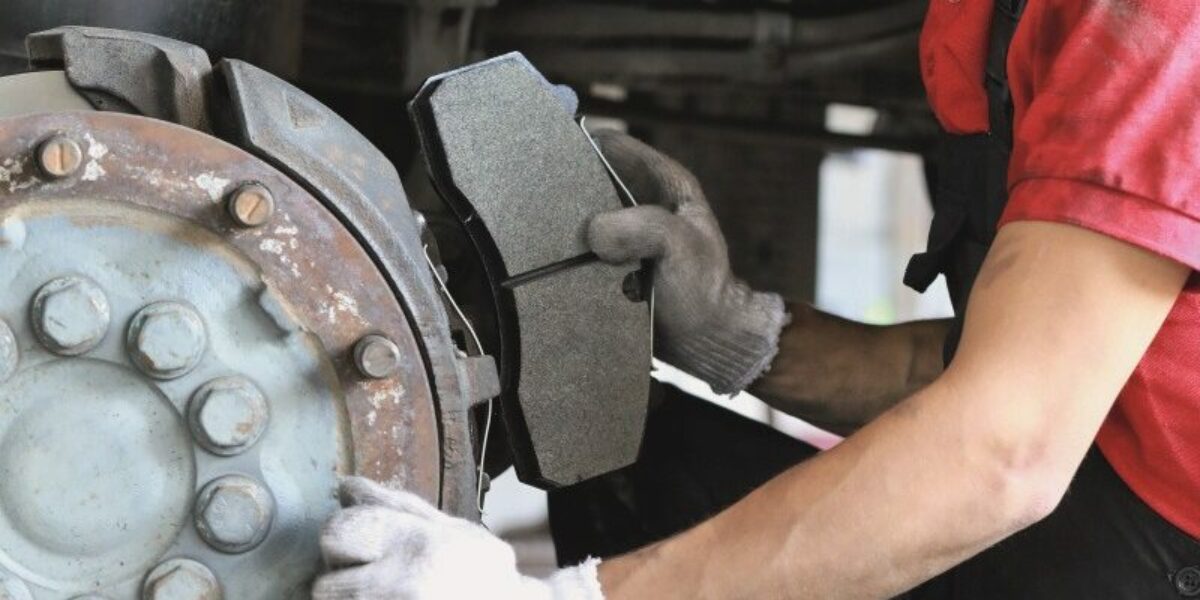
Bremsbelag ist nicht gleich Bremsbelag
Bremsen für Lkw und Trailer sind heute im Regelfall als Scheibenbremsen ausgeführt und enormen Belastungen ausgesetzt. Bei den Belägen selbst, gibt es deutliche Unterschiede. Was also zeichnet einen hochwertigen Bremsbelag aus?
Die wichtigsten Kriterien um die Qualität eines Bremsbelags festzustellen ist die Belag-Festigkeit, die Anbindung zur Trägerplatte und das Verschleißverhalten. Dabei ist die Homologation nach ECE-R90 allein nicht unbedingt ein Hinweis auf hohe Qualität, die Norm definiert den technischen Mindeststandard. „Bei TMD-Friction müssen Bremsenteile weit höheren Qualitätsanforderungen entsprechen, um eine interne Freigabe zu erhalten“, erzählt Bernd Rohrberg, Vice President Global Customer Team & R&D Commercial Vehicles. So unterzieht man die Bremsbeläge bereits in der Entwicklungsphase verschärften Tests und Simulationen, wie beispielsweise einer Bergabfahrt, bei der Bremsscheibentemperaturen von über 900 °C auftreten. „So vergewissern wir uns, dass wir die Bremsleistung und die Belag-Festigkeit auch unter extremen Bedingungen gewährleisten können.“ Was die Verbindung von Reibmaterial und (Leichtbau-)Trägerplatte angeht, kommen neben einem Klebersystem auch noch mechanische Anbindungen zum Einsatz. Aufgeschweißte oder auch integrierte Pins, die in das Reibmaterial hineinragen, sollen für eine zusätzliche Haftung und Verstärkung des Belag-Systems sorgen.
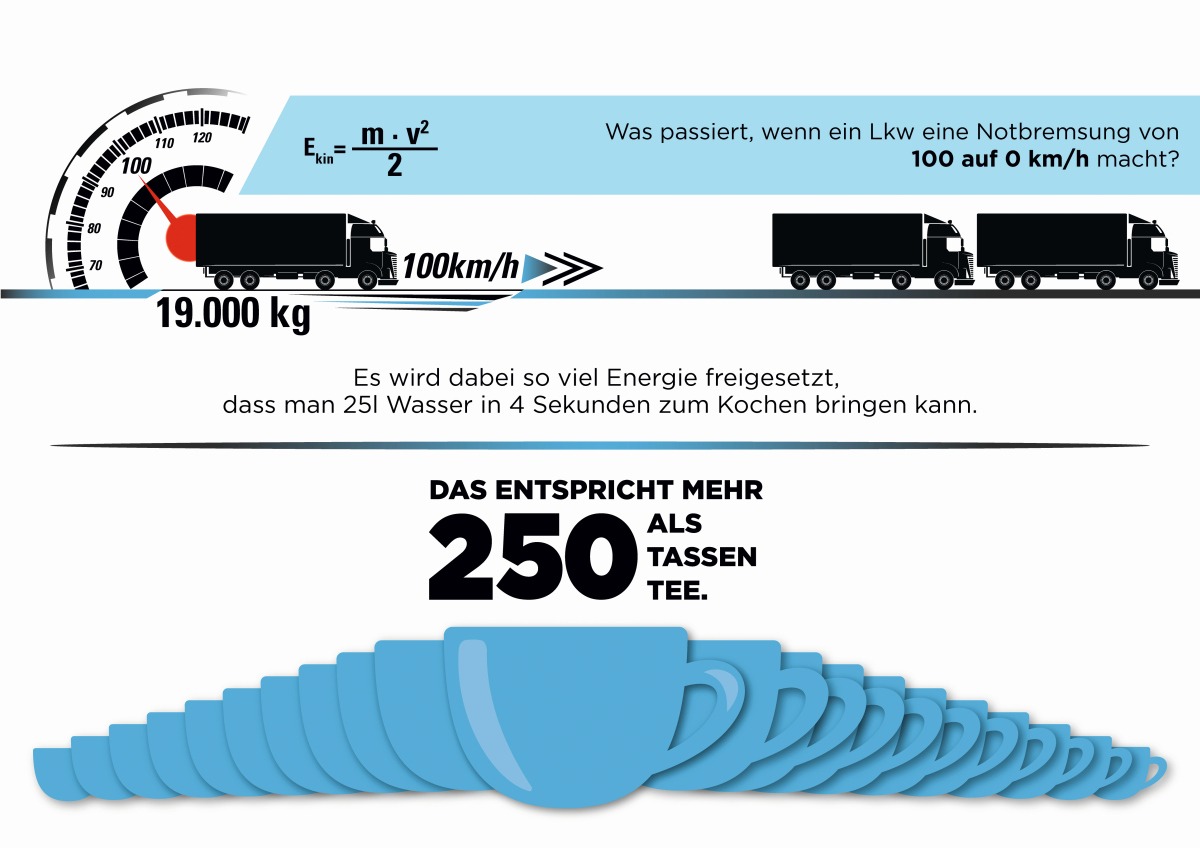
Einfluss auf den Reibpartner
Ein Bremsbelag hat direkten Einfluss auf die Bremsscheibe, beispielsweise auf das Rissverhalten. Durch die Materialzusammensetzung und die physikalischen Eigenschaften der verwendeten Komponenten möchte TMD-Friction sicherstellen, dass dieser Einfluss nur minimal ist. „Generell lassen sich Schädigungen der Bremsscheiben auch bei regulärem Einsatz nie vollständig verhindern. Wir stellen durch unsere Maßnahmen jedoch sicher, dass wir etwaige Einflüsse so gering wie möglich halten“, so Rohrberg. Wie in einer funktionierenden Beziehung, müssen die Reibpartner zueinander passen. Die Materialmischung des Bremsbelags ist im Optimalfall auf die jeweilige Bremsscheibe abgestimmt. Dies gilt laut TMD-Friction für die Erstausrüstung, wie auch für den Aftermarket.
Wo Reibung entsteht, entsteht Abrieb, beziehungsweise Feinstaub. Das Thema rückt aus Gesundheitsgesichtspunkten immer mehr in den Fokus. Beispielsweise bietet der Filter-Spezialist Mann+Hummel bereits einen Bremsstaubfilter an. Gesetzliche Vorgaben zur Höhe von Bremsstaub-Emissionen gibt es bisher nicht. Das Verschleißverhalten, sprich die Haltbarkeit, spielt eine große Rolle, denn es gilt: Je weniger Material verschlissen wird, desto weniger Feinstaub wird freigesetzt.
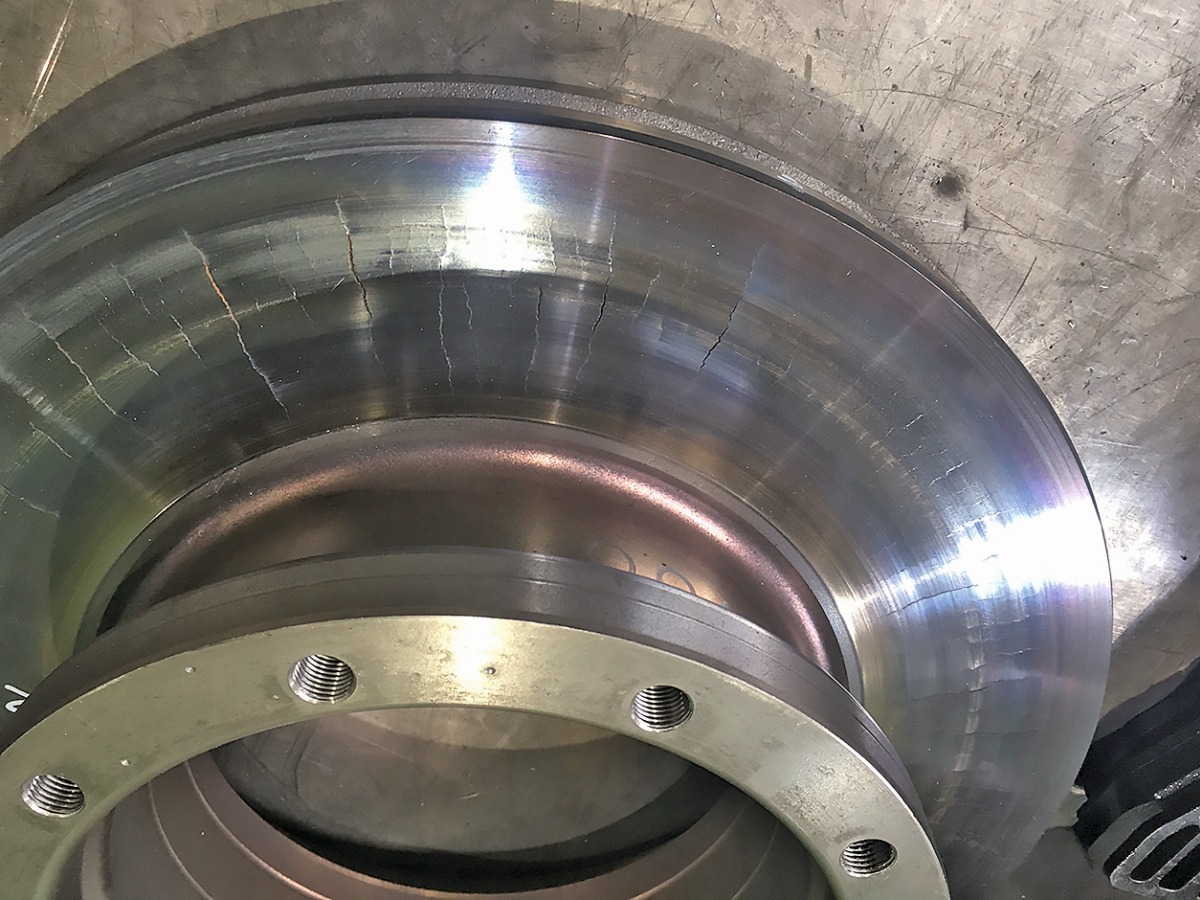
Die Materialzusammensetzung
Die konkrete Zusammensetzung eines Bremsbelages ist ein gut gehütetes Geheimnis. Auch Bernd Rohrberg möchte sich nicht im Detail äußern. „Grundsätzlich aber werden alle Rohstoffe, die wir haben – und das sind im Moment in etwa 300 – in vier Gruppen eingeteilt: Metalle, Schmierstoffe, organische Bestandteile und Füllstoffe. Um die gewünschten Eigenschaften zu erfüllen, kombinieren wir für ein Belagmaterial mehr als 20 verschiedene Rohstoffe aus den jeweiligen Gruppen miteinander. Dabei variieren sowohl die Rohstoffmengen als auch die Anzahl der verwendeten Rohstoffgruppen.“ Aufgrund der Komplexität der Materialzusammensetzung ist die Entwicklung eines neuen Belag-Materials, inklusive der Erprobung, ein langwieriges Projekt. Laut TMD-Friction dauert es bis zu drei Jahre bis zur Marktreife.
Der Herstellungsprozess
Da auch durch die Herstellung die Belag-Eigenschaften stark beeinflusst werden, muss der Ablaufprozess genauestens definiert werden. Im ersten Schritt erfolgt die Mischung der einzelnen Rohstoffe unter exakten Vorgaben und Rahmenbedingungen. Daraufhin wird die Materialmischung mit den Trägerplatten aus Metall unter hohem Druck verpresst. Um die chemischen Reaktionen der Rohstoffe abzuschließen, erfolgt jetzt eine Wärmebehandlung. Am Ende bekommen die Beläge ihre Dimension, Phasen werden je nach Kundenanforderung eingeschliffen. Die Lackierung und Kennzeichnung schließt den Produktionsvorgang ab. Was allzu simpel klingt, ist ein hochkomplexer Vorgang.
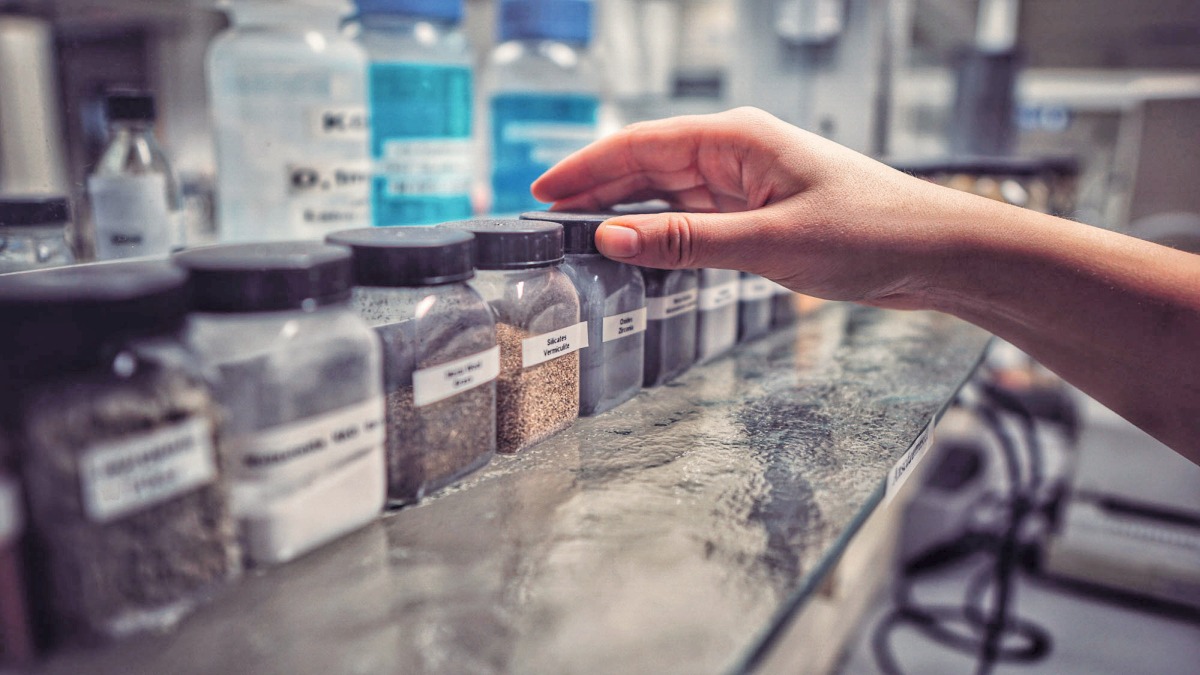
Kopierschutz/Montage
Auch Bremsbeläge werden oftmals kopiert und über unterschiedliche Quellen auf dem Markt zu Niedrigpreisen angeboten. „Im Rahmen unserer Initiative ‚Fighting the fakes‘ engagieren wir uns dafür, das Plagiatsrisiko für die Werkstatt so gering wie möglich zu halten, denn Plagiate können auch für Fachleute teilweise schwer zu erkennen sein“, so Oliver Hill, Global Sales & Marketing Director IAM Commercial Vehicles bei TMD-Friction. Wenn es bei uns zu Reklamationen kommt, sind diese jedoch häufig auf eine unsachgemäße Montage zurückzuführen. So raten die Experten, dass auf jeden Fall immer mit der notwendigen Sorgfalt, am besten ohne Zeitdruck vorgegangen wird. Auch die Messung der Bremsscheibendicke muss bei Zweifeln genauestens vorgenommen werden. Unabdingbar ist zudem ein sauberer und heller Arbeitsplatz.
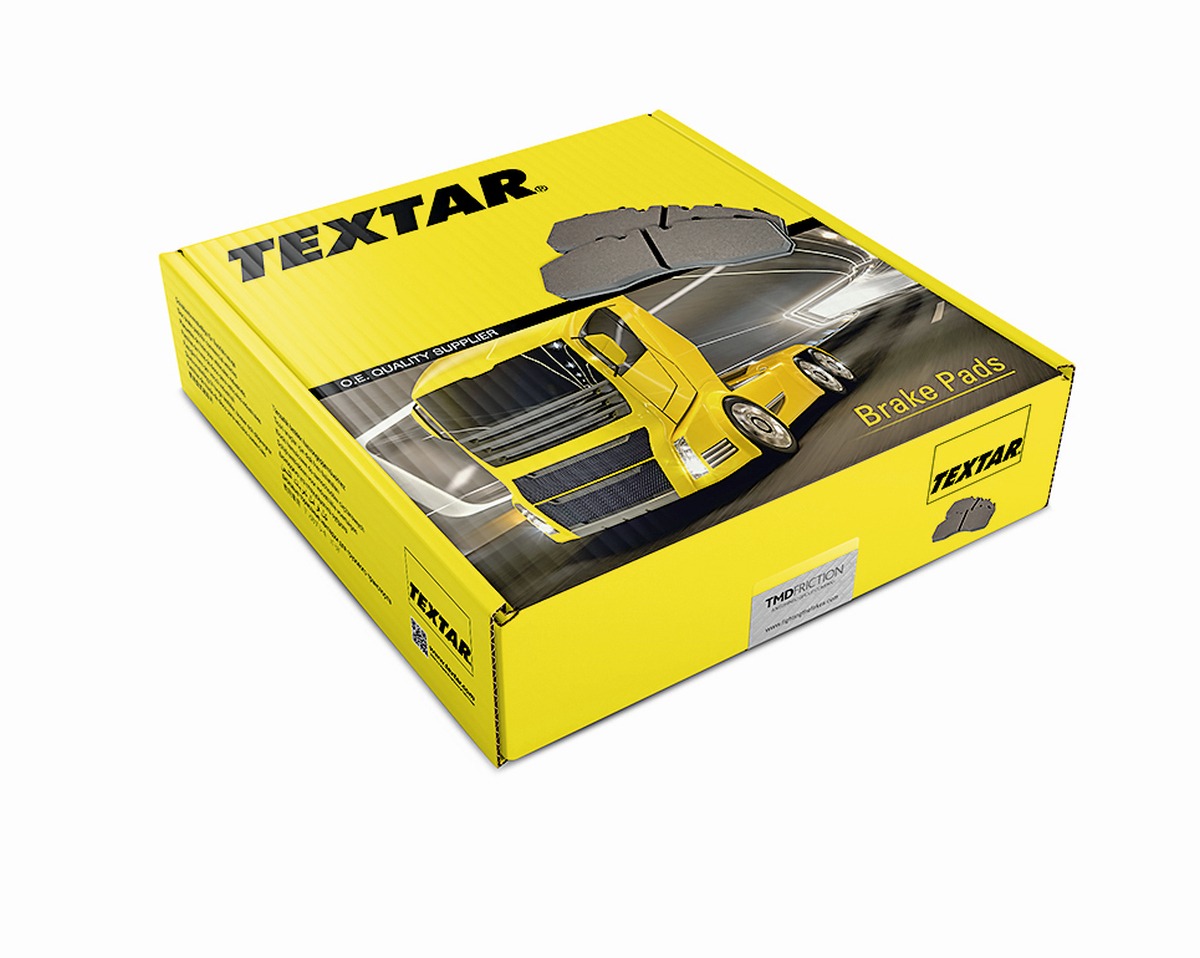
Ein konkretes Beispiel, bei dem es immer wieder zu Montagefehlern kommt, ist die Sicherstellung des korrekten Lüftspiels nach der Belagmontage. Es handelt sich um Bereiche von 0,7 – 1,0 Millimetern, die aber genau nach Herstellervorgaben eingehalten werden müssen, um ein gutes Verschleißverhalten zu gewährleisten. Auch die automatische Nachstellung des Bremssattels kann durch ein nicht korrekt eingestelltes Lüftspiel ihre Funktion verlieren.
Den Beitrag finden Sie auch in der Print-Ausgabe 1-2/21 der Krafthand-Truck.