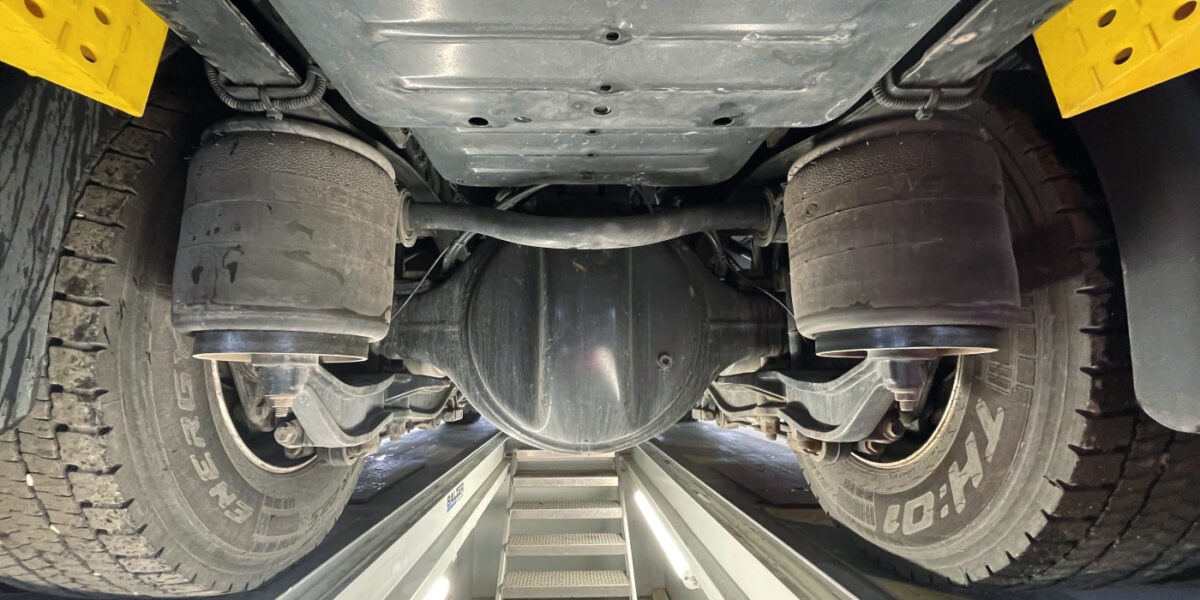
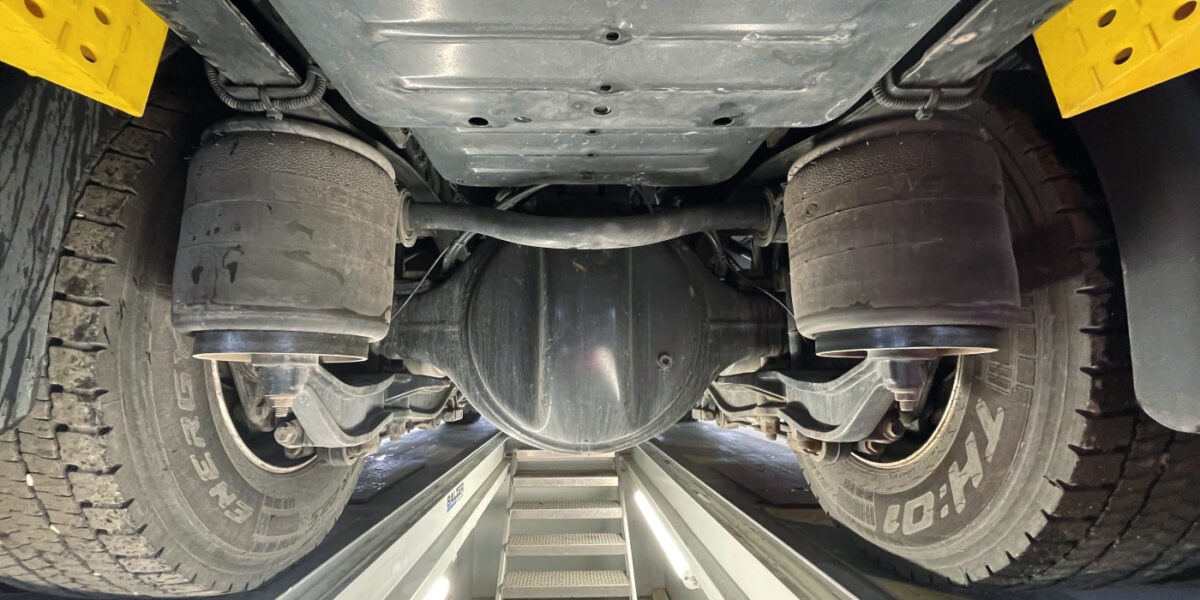
Ständig unter Druck
Luftfedern sind zuverlässige Komponenten, weshalb der Werkstattfachmann Ihnen beim Fahrzeugcheck oft zu wenig Aufmerksamkeit schenkt. Doch Federbälge altern und verlieren mit der Zeit Luft. Mitunter kommt es zu anderen, drastischeren Schäden. Ein rechtzeitiger Ersatz des Federbalgs kann einen plötzlichen Luftverlust und gefährliche Folgen verhindern.
Luftfedern sind Verschleißteile
Unter normalen Betriebsbedingungen und mit einem Mindestmaß an Wartung halten Luftfedern mehrere Jahre und überstehen dabei klaglos tausende von Kilometer. Prinzipiell sind Federbälge so verschleißarm, dass sie andere Fahrwerkskomponenten wie Lagerbuchsen, Stoßdämpfer, Ausgleichsventile oder Regler oft deutlich überdauern. Dennoch gehören sie zu den klassischen Verschleißteilen im Fahrwerk von Lkw, Anhängern und Aufliegern, welche regelmäßig die Aufmerksamkeit des Werkstattfachmanns erfordern. Und obwohl der Tausch einer Luftfeder kein Hexenwerk ist, gibt es wichtige Punkte zu beachten.
Ursachen für Defekte an Luftfederbälgen
Luftfederbalg-Defekte sind häufig auf eine mangelhafte Wartung des Federungssystems beziehungsweise des Gesamtfahrzeugs zurückzuführen. Ein unsachgemäßer Einsatz der Zugmaschine und des Trailers kommt hinzu. Zu den typischen „Luftbalg-Killern“ gehören eine häufige Überladung, lange Fahrtstrecken mit maximaler Ausdehnung, extremer Baustellenbetrieb, schlechte Fahrbahnoberflächen (tiefe Schlaglöcher, spitze Kieselsteine, schmirgelnder Straßenstaub) sowie harte Stöße in komprimiertem Zustand. Hinzu kommen defekte Stoßdämpfer (bei Undichtigkeiten: Kontakt mit Hydrauliköl), ein falsch justiertes Fahrzeugniveau (zu hoch/zu niedrig), ein zu hoch/zu niedrig eingestellter oder defekter Druckregler oder ein häufiges Entleeren des Luftfederbalgs im Stand aufgrund einer undichten Luftanlage. Auch Überdehnungen beim Anheben im Falle eines defekten Anschlags (zum Beispiel bei Reparaturen oder bei der Bahnverladung), Korrosion an den Metall-Komponenten, ein falscher Luftfedertyp (zu lang/zu kurz, zu geringer Gewichtsbereich) und aggressives Streusalz gehören zu den Ursachen eines Defekts. Last but not least kommen Verunreinigungen durch Betriebsflüssigkeiten (Öle, Fette, Dieselkraftstoff, Brems- oder Kühlflüssigkeiten), eine hohe UV-Belastung, die unsachgemäße Reinigung (scharfer Hochdruckreiniger-Strahl, ungeeignete Reinigungsmittel (zugelassen sind Seifenlauge, Methanol, Äthanol und Isopropylalkohol)) und letztendlich die natürliche Alterung des Gummis hinzu.
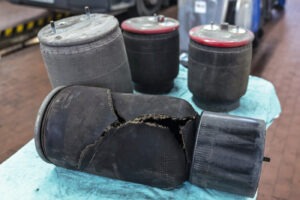
Präventiv prüfen
„Den Luftfederbälgen wird häufig zu wenig Beachtung geschenkt. Plötzlich funktionieren sie nicht mehr oder nicht mehr in vollem Umfang“, weiß auch Daniel Most, Gebietsverkaufsleiter beim Nutzfahrzeugteile-Spezialisten Auger. Der Auflieger lasse sich dann nur noch schlecht ab- und aufsatteln, unterwegs könne die Ladung in Mitleidenschaft gezogen werden, weil die Luftfederung heftige Stöße nicht mehr absorbiere. „Probleme mit den Luftfedern kosten Zeit und Geld. Wenn eine Luftfederung komplett ausfällt, dann steht der Lkw“, so Most. Der Verkaufsfachmann empfiehlt regelmäßig einen Blick auf die Luftfederbälge. Wenn das Gummi porös werde oder der Balg Schäden aufweise, sei spätestens Zeit für Ersatz. Beginnende Undichtigkeiten lassen sich im Übrigen mit Seifenlauge oder einem professionellen Lecksuchspray aufspüren.
Checkliste Luftfederung
Bei schwierigen Betriebsbedingungen und Fehlern am Fahrwerk kann es zu vorzeitigem Verschleiß der Luftfederbälge kommen. Die Experten von Firestone Airide empfehlen beim Check das Abarbeiten folgender Punkte:
- Luftfederbälge auf ungleichmäßigen Verschleiß und Wärmerisse untersuchen.
- Druckleitungen prüfen und dabei darauf achten, dass sie den Balg nicht berühren (Scheuerstellen!).
- Sicherstellen, dass bei einer maximal gefüllten Luftfeder genügend Abstand zu den umliegenden Komponenten (Stoßdämpfer, Achsteile, Chassis) bleibt.
- Kolben der Luftfeder auf Materialansammlungen prüfen und Steine, Staub, Schmutz entfernen.
- Das fahrzeugspezifische Fahrniveau (Fahrhöhe) prüfen und korrekt justieren. Dabei ist das Niveau je nach Herstellervorgabe in beladenem oder unbeladenem Zustand zu ermitteln.
- Prüfen der korrekten Funktion der Ausgleichs- beziehungsweise Höheneinstell-Ventile. Bei Bedarf müssen die Ventile gereinigt oder gewechselt werden.
- Prüfen der Stoßdämpfer und dabei auf die richtige Größe (Länge, Durchmesser, Befestigungsart), auslaufendes Hydrauliköl sowie defekte oder verschlissene Endanschläge und verbogene Wulstplatten achten. Im Falle eines Defekts ist der Dämpfer zu erneuern.
- Prüfen aller Muttern und Schrauben auf korrekten Drehmomentanzug.
Quelle: Firestone Airide
Vorzeitiger Ausfall hat oft andere Ursachen
Oft liegen die Gründe für einen vorzeitigen Ausfall eines Luftfederbalgs jedoch nicht am Balg selbst, ein Defekt an der Peripherie ist der Grund. „Ist der Defekt auf ein Problem innerhalb des Federungssystems zurückzuführen, so wird auch die neue Luftfeder bald wieder versagen, falls die Ursache nicht behoben wird“, so die Fachleute von Firestone Airide. „Da jede einzelne Feder im Werk genau druckgeprüft wird, handelt es sich bei vorzeitigen Ausfällen und den damit verbundenen Garantie-Forderungen, meist nicht um Produktmängel, sondern um einen Defekt aufgrund anderer Probleme mit der Federung. Manchmal sind aber auch simple Einbaufehler der Grund für einen vorzeitigen Ausfall.“
Der Tausch der Luftfedern
Obwohl der Austausch von Luftfedern prinzipiell nicht kompliziert ist, erfreut sich die Arbeit nicht großer Beliebtheit. Der vermeintliche Routinejob verlangt neben Know-how auch Geschick. Unbeliebt ist der Balgwechsel vor allem auch deshalb, weil das Krempeln des neuen Balgs meist mühsam ist. Die Arbeit verlangt den Spezialisten von Contitech zufolge Kraft und Erfahrung gleichermaßen. Nicht zuletzt deshalb muss sich der Nfz-Profi in jedem Fall an die Montagevorschriften des Fahrzeugherstellers halten.
Montagetipps
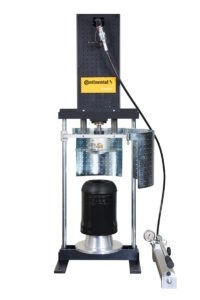
Bevor man das Luftfedersystem entlüften kann, muss das Fahrzeug professionell abgesichert und die Achse entlastet werden. Kompressor und Zündung bleiben während den Arbeiten ausgeschaltet. Zum Entlüften schraubt man das Ventil heraus. Damit kein Schmutz eindringen kann, packt man es am besten in eine kleine Plastiktüte. Anschließend löst man sämtliche Schrauben, zunächst zwischen Luftfeder und Chassis, anschließend zwischen Luftfeder und Achse.
Idealerweise ersetzt man die komplette Luftfedereinheit. Die neue Luftfeder wird zunächst oben am Chassis befestigt, dann zieht man den Kolben nach unten bis zur Anlage heraus. Falls dies schwer geht, kann man mit einer Druckluftpistole (maximal 0,3 bar!) nachhelfen. Beim Festziehen der Befestigungsschrauben und des Luftventils sind unbedingt die vom Hersteller vorgegebenen Anzugsdrehmomente einzuhalten. Schließlich kann man die Bälge mit dem vorgeschriebenen Betriebsdruck füllen, die Abstützhilfen ausbauen und das Fahrzeug zurück in die Fahrposition bringen.
Den Beitrag finden Sie auch in der Print-Ausgabe 2-2023 der Krafthand-Truck.