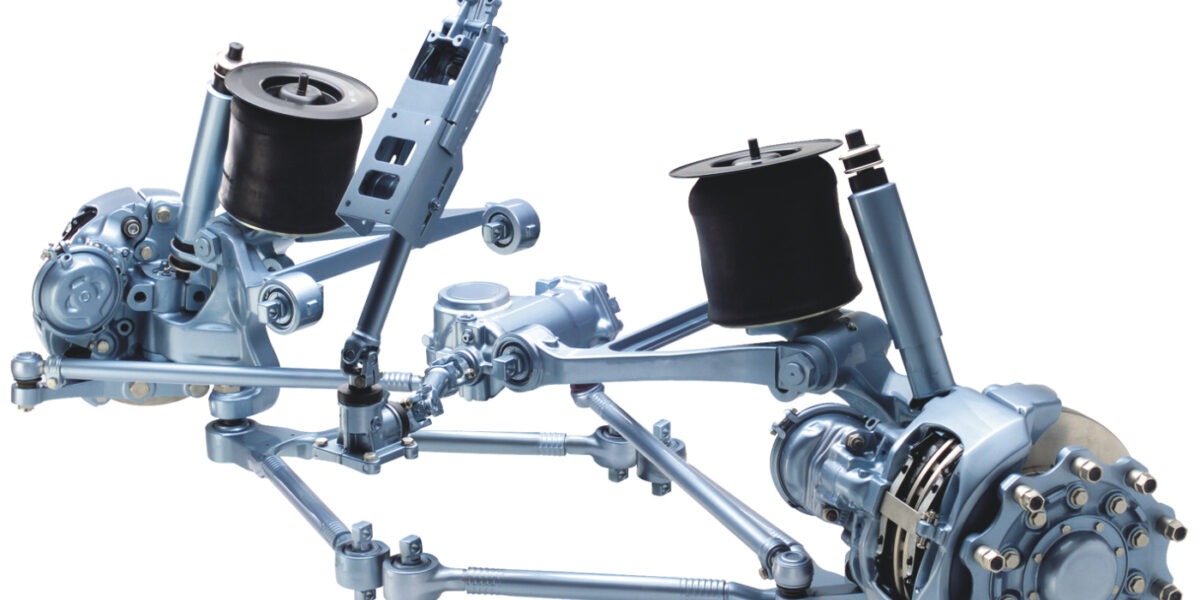
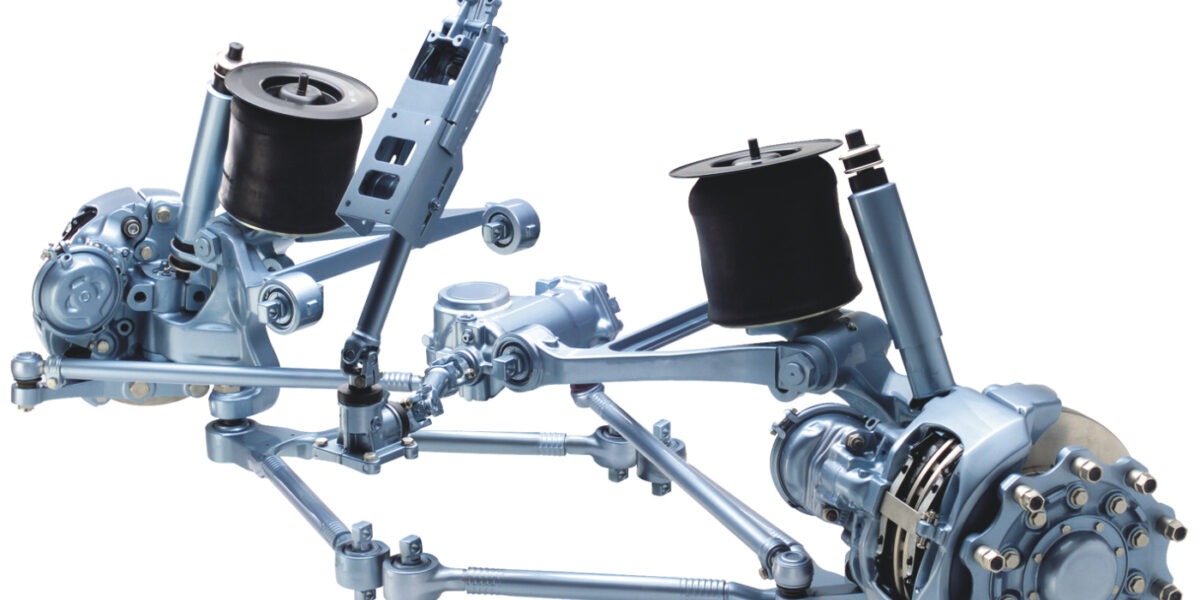
Die Technik und Wartung von Nfz-Lenksystemen
Perfekter Geradeauslauf, volle Fahrzeugkontrolle unter allen Bedingungen, alles ohne großen Kraftaufwand. Mit einem modernen Lenksystem ist das kein Problem. Doch extreme Einsatzbedingungen, klassischer Betriebsverschleiß und Unfallfolgen können das Zusammenspiel im Lenksystem stören.
Die Lenkung ist tatsächlich die Seele eines Nutzfahrzeugs. Mit ihr steht der Fahrer ständig in Kontakt, spürt den Zustand der Straße, spürt wie das Fahrzeug reagiert. Sie soll einerseits leichtgängig, komfortabel und präzise arbeiten, andererseits möglichst viel Rückmeldung über den Straßenzustand liefern. Letztendlich muss die Lenkung jederzeit eine sichere Teilnahme am Straßenverkehr gewährleisten. Damit das funktioniert, müssen die mechanischen, hydraulischen und elektronischen Komponenten eines modernen Lenksystems optimal zusammenspielen.
Hydraulisch lenken
Obwohl es mittlerweile elektrohydraulische und bereits vollelektrische Lenksysteme (Steer-by-Wire) gibt, ist die hydraulische Lenkung, bestehend aus Lenkgetriebe und Lenkhilfepumpe (auch: Lenkhelf- oder Lenkungspumpe), immer noch die am weitesten verbreitete Variante. Der Grundaufbau hat sich über die Jahre kaum verändert.
Während bei Transportern und leichteren Nutzfahrzeugen überwiegend Zahnstangenlenkungen zum Einsatz kommen, sind mittelschwere und schwere Nutzfahrzeuge klassischerweise mit einer hydraulischen Kugelumlauflenkung (auch: Kugelmutterlenkung) ausgerüstet. Beide Varianten gelten prinzipiell als wartungsfrei. Im Falle eines Defekts sind allerdings die Fachkenntnisse des Nutzfahrzeugprofis gefragt.
Die Kugelumlauflenkung
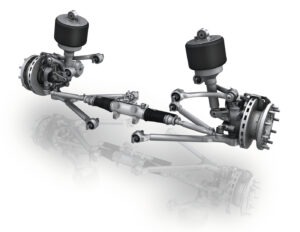
Bei der Kugelumlauflenkung (auch Kugelmutterlenkung) wird die Lenkbewegung des Fahrers über den Lenkspindelanschluss auf die Schnecke des Lenkgetriebes übertragen und über ein Kugelgewinde mit endloser Kugelkette in eine Axialbewegung des Kolbens umgewandelt. Gleichzeitig versetzt eine Verzahnung die rechtwinklig zur Kolben-Längsachse angeordnete Segmentwelle in eine Drehbewegung. Der auf der Segmentwelle befestigte Lenkstockhebel bewegt das zu den Radlenkhebeln führende Lenkgestänge und bewirkt so einen Lenkeinschlag der Räder. Der von der Lenkungspumpe geförderte Ölstrom gelangt über Zulaufkanäle zu den Steuernuten des Drehschieberventils und strömt in dessen Neutralstellung über die offenen Steuerkanten wieder in den Rücklauf und zurück zum Ölbehälter.
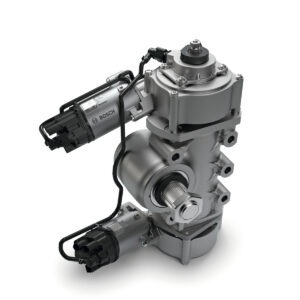
Beim Drehen des Lenkrads verdreht sich der Drehschieber gegenüber der Steuerungsbuchse, wodurch der Ölstrom in den die Drehbewegung unterstützenden Zylinderraum gelangt und so die gewünschte hydraulische Unterstützung erzeugt. Eine integrierte hydraulische Lenkbegrenzung schützt Lenkgestänge, Radanschlag und Lenkungspumpe vor Schäden. Neben Ein- und Zweikreis-Varianten gibt es auch Ausführungen mit angeflanschtem Winkelgetriebe. Letzteres ist bei Nutzfahrzeugen notwendig, wenn durch die Anordnung des Lenkgetriebes keine direkte Anbindung der Lenksäule möglich ist.
Das Winkelgetriebe besteht im Wesentlichen aus je einer wälzgelagerten An- und Antriebswelle inklusive Kegelverzahnung. Üblicherweise tragen beide Wellen ein geradverzahntes Kegelrad mit gleicher Zähnezahl, wodurch sich eine 1:1-Übersetzung ergibt. Winkelgetriebe sind üblicherweise dauergeschmiert und somit wartungsfrei. Standard ist ein Achswinkel von 90°, es gibt aber auch Varianten mit bis zu 120°.
Hydraulische Lenkhilfepumpen
Bei den hydraulischen Lenkhilfepumpen haben Flügelzellenpumpen den bislang üblichen Zahnradpumpen aufgrund der höheren Betriebsdrehzahl, der geringere Förderstrompulsation sowie des geringeren Betriebsgeräusches und der möglichen Kraftstoffeinsparung, den Rang abgelaufen. Flügelzellenpumpen bestehen aus einem Stator und einem dazu exzentrisch angeordneten Rotor, welcher Aussparungen besitzt, in denen sich die Flügel befinden. Diese werden im Betrieb durch Feder- und Fliehkräfte nach außen gegen den Stator gedrückt. Läuft die Pumpe, vergrößern sich die Räume zwischen den Flügeln im Saugbereich, sodass Hydraulikflüssigkeit angesaugt wird. Auf der gegenüberliegenden Seite wird das Öl in den Druckbereich gepresst, da sich die Räume zwischen den Flügeln wieder verkleinern.
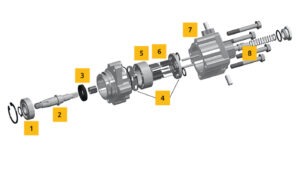
Darüber hinaus gibt es so genannte Tandem-Pumpen, bei denen sich zwei Pumpen für unterschiedliche Medien in einem Gehäuse befinden. Eine davon ist für den Druck im Lenksystem verantwortlich, die andere fördert je nach Einsatzzweck Dieselkraftstoff zur Einspritzanlage oder erzeugt ein Vakuum. Beide Pumpen werden von einem gemeinsamen Antriebsriemen angetrieben.
Probleme mit der Hydraulik
Lenkhilfepumpen sind prinzipiell standfest, zumindest solange sie mit ausreichend sauberem Hydraulik-Öl versorgt und geschmiert werden. Probleme mit der Lenkhilfepumpe machen sich üblicherweise durch schwergängiges Lenken oder Arbeitsgeräusche wie Zischen, Quietschen, Rattern bemerkbar. Die Ursachen können vielfältig sein. Gelangt beispielsweise Luft durch Undichtigkeiten im Ansaugbereich (zum Beispiel durch eine gelockerte Hydraulikleitung oder aufgrund einer mangelhaften Entlüftung nach einer vorausgegangenen Reparatur) ins System, saugt die Pumpe die Luft an, wodurch der Schmierfilm abreißt und die Pumpe bis zum Totalschaden trocken läuft. Bei hohen Drehzahlen und unter hoher Belastung kann ein solcher Defekt innerhalb kürzester Zeit eintreten.
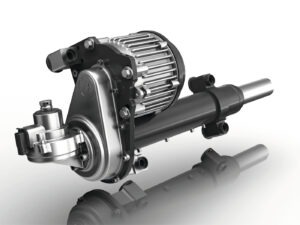
Auch Probleme mit dem Hydrauliköl selbst können die Pumpe schädigen und sie zerstören. Ein silbriges Aussehen des Schmierstoffs deutet beispielsweise auf Metallabrieb durch Verschleiß oder zeitweiliges, längeres Trockenlaufen hin. Ein Geruch nach ‚Verbranntem‘ zeugt von einer thermischen Überbeanspruchung, etwa weil der Fahrer beim Rangieren die Lenkung extrem oft zum Anschlag bringt. Zudem kann das Druckbegrenzungsventil der hydraulischen Lenkbegrenzung am Lenkanschlag defekt sein, oder es wurde nach einem Lenkgetriebeersatz falsch eingestellt. Emulsionsähnliches (milchiges) Aussehen des Hydrauliköls weist indes auf einen erhöhten Wasseranteil hin (zum Beispiel durch falschen Einsatz eines Hochdruckstrahlers, undichte Ausgleichsbehälter oder vergessene Verschlussdeckel). Eine unnormale Schaumbildung kann die Folge von überaltertem oder falschem Hydrauliköl sein.
Bei Tandem-Pumpen, welche Kraftstoff fördern, gibt es systembedingt einen weiteren Ausfallgrund: etwa, wenn verschmutzter Diesel in die Kraftstofffördereinheit gerät und es deswegen zu einem Festfressen kommt. Dann ist in der Regel auch keine Lenkkraftunterstützung mehr möglich.
Das Lenksystem prüfen
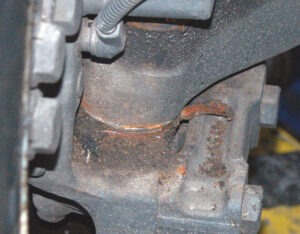
Üblicherweise überprüft der Lkw-Profi die Funktion des Lenksystems im Rahmen der regelmäßigen Wartungsintervalle oder bei der Sicherheitsprüfung (SP) nach § 29 StVZO. Zur Prüfung gehört unter anderem der Check des Ölstands, eine Sichtprüfung auf Undichtigkeiten sowie die Prüfung des Spiels von Kugelgelenken, Lenkungsbuchsen, Kardangelenken, Teleskopwellen und Lenksäulenlagern in radfreiem sowie belasteten Zustand auf der Hebebühne oder über der Montagegrube. Dies geschieht idealerweise mit einem Gelenkspieltester. Hinzu kommt der Check des Lenk- sowie gegebenenfalls des Umlenkgetriebes. Zudem darf ein Blick auf die Spannung des Antriebsriemens und die Funktion der Spannelemente und Rollen nicht fehlen. Bei manchen Lenksystemen ist zudem der Öl(fein)filter gemäß Herstellervorgabe zu reinigen oder zu ersetzen. Während der Probefahrt achtet der Nutzfahrzeugprofi außerdem auf die Rückstellung der Lenkung in die Neutralstellung, auf Ratter- oder Klemmstellen, abnormale Geräusche und auf den Lenkwiderstand an sich.
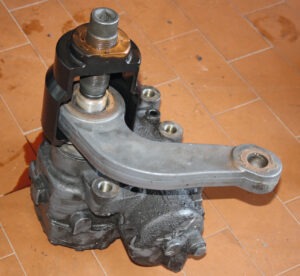
Im Falle einer Beanstandung oder eines Defekts, ist neben den genannten Checks eine Druckprüfung des Hydraulikkreislaufs nach Herstellervorgabe vonnöten, um sich ein Bild von der (noch verbliebenen) Leistungsfähigkeit der Lenkhilfepumpe und der Funktion des Ventilsystems zu verschaffen. Die Prüfung kann mit einem Einfach-Manometer oder mit einem speziellen Servotester erfolgen. Ist der ermittelte Arbeits-/Maximaldruck zu gering, ist die Lenkungspumpe zu ersetzen.
Spülen und entlüften
Ist die Servopumpe defekt, können Verunreinigungen wie Metallspäne ins Hydrauliksystem gelangt sein. Daher muss der Werkstattfachmann nach dem Ausbau der defekten Servopumpe das gesamte Hydrauliksystem nach Herstellervorschrift mit frischem Hydraulik- oder speziellem Spülöl reinigen, bis sämtliche Verunreinigungen entfernt sind. Ansonsten besteht die Gefahr, dass die neue Pumpe aufgrund von alten Rückständen wieder Schaden nimmt. Nach dem Spülen und dem Einbau der neuen Pumpe ist das Hydrauliksystem mit frischem, sauberem Hydraulik-Öl zu befüllen und gemäß der Herstellerangaben zu entlüften. Üblicherweise bewegt man dazu das Lenkgetriebe bei ‚Motor im Leerlauf‘ mehrfach von Anschlag zu Anschlag, bis im Ausgleichsbehälter keine Luftblasen mehr aufsteigen.
Erst das Fahrwerk, dann das Assistenzsystem
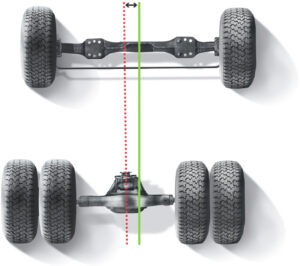
Radar- und kamerabasierte Fahrerassistenzsysteme (FAS) wie Abstandsregeltempomat (ACC), Notbremsassistent (AEBS) oder Spurverlassenswarner (LDWS) gehören zur Standardausstattung vieler Lkw. Dadurch kommt der Nutzfahrzeug-Profi auch bei Reparaturarbeiten am Lenkungssystem mit FAS in Kontakt, selbst wenn er nicht direkt daran arbeitet. Das Kalibrieren von FAS ist also nicht nur nach dem Erneuern der Windschutzscheibe oder eines Radarsensors notwendig, sondern auch nach dem Tausch des Lenkgetriebes oder einer Lenk- oder Spurstange. Prinzipiell gilt, dass nach Arbeiten, welche die Blickrichtung eines FAS-Sensors beeinflussen könnten, auch eine Neukalibrierung der betroffenen Systeme erforderlich ist. Andernfalls besteht das Risiko, dass die FAS nicht (mehr) vorschriftsmäßig funktionieren und es im Extremfall zu gefährlichen Situationen kommt.
Zusätzlich empfehlen FAS-Experten, vor dem Kalibrieren die Fahrwerkseinstellung zu überprüfen, um sicherzustellen, dass die geometrische Fahrachse, auf der sich der Lkw auf der Straße bewegt, in Ordnung ist. Geprüft wird die Achsgeometrie mit einem Laser- oder Kameramesssystem, wobei zunächst von der Hinterachse aus die Rahmenmittellinie, also die geometrische Fahr- oder Schubachse, ermittelt wird. Erst wenn sichergestellt ist, dass diese den Herstellervorgaben entspricht, lassen sich weitere Parameter korrigieren.
Den Beitrag finden Sie auch in der Print-Ausgabe 3-2023 der Krafthand-Truck.