Der Hochdrucksensor
Der Hochdruck ist die Haupteingangsgröße für die Regelung des Kraftstoffsystemdrucks. Dazu ist im Hochdruckbereich, meistens am Rail, der Hochdruck- oder auch Raildrucksensor verbaut. In einem seltenen Fall, beim GDI (Mitsubishi) der ersten Generation, ist dies am Druckreglergehäuse der Fall.
Die Sensoren werden mit einem streng einzuhaltenden Drehmoment im Rail befestigt, da nur so die Dichtheit der Flächen am Sensor in der Railbohrung zueinander gewährleistet ist.
Korrektes Drehmoment
Wenn die Sensoren wieder verwendet werden, muss das gleiche Drehmoment wie beim neuen Sensor angewandt werden. Zu festes Anziehen, um eine zuverlässige Dichtheit zu gewährleisten, kann zur Rissbildung vor allem in Aluminiumrails führen.
Bei einigen Systemen ist sogar der Einzeltausch des Sensors nicht mehr zulässig. In dem Fall muss das gesamte Rail erneuert werden. Der Austausch eines Hochdrucksensors ist dem Motorsteuergerät bei neueren Systemen mit dem Diagnosetester mitzuteilen.
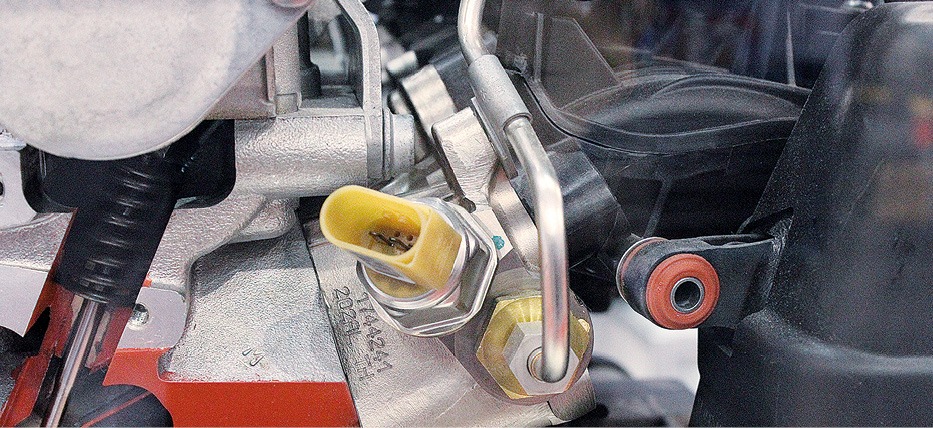
Das Motorsteuergerät überschreibt dann die alten Adaptionswerte mit den neuen. Diese werden dann in die nächsten Fahrzyklen aufgenommen. Ein probehalber Quertausch eines Sensors kann daher nicht zielführend sein.
Hochdrucksensoren haben die Funktion, den aktuellen Kraftstoffdruck im Verteilerrohr (Rail) zu erfassen und nahezu in Echtzeit an das Steuergerät zu senden, also ohne nennenswerte Zeitverzögerung zwischen Messung und Übermittlung des Signals.
Aktive Sensoren
Es werden ausschließlich aktive Sensoren eingesetzt, die zumeist an den äußeren Kontakten mit einer Betriebsspannung von 5 V versorgt werden. Das Mess-Signal wird im inneren des Sensors durch die druckbedingte Verformung einer Stahlmembrane oder in selteneren Fällen von einem Piezokristall erzeugt.
Da das Grundsignal zu schwach und zu störanfällig ist, wird es von einem anwendungsspezifischen Schaltkreis aufbereitet und verstärkt, um als analoges Spannungssignal von 0,2–4,80 V an das Motorsteuergerät übertragen zu werden. Das Signal ist dann am mittleren Anschluss messbar.
Am Sensor sollten keine Widerstandsmessungen durchgeführt werden, da im Inneren eine sensible Elektronik arbeitet. Der Spannungsverlauf ist sehr von der Auslegung des Sensors und dem maximalen Systemdruck abhängig, den er in der Anlage messen soll. Bei eingeschalteter Zündung, wo bei den meisten Systemen nicht mehr als der Vorförderdruck im Rail aufgebaut wird, sollte sich eine Signalspannung von mindestens 0,5 V ergeben.
Die Leerlaufdrücke liegen meist bei 40–70 bar, was an einer Siemensanlage der ersten Generation einer Signalspannung von 2,4 – 2,7 V entspricht.

Bei den Bosch-Anlagen entspricht dies etwa 1,9 V. Beim Mitsubishi GDI werden im Leerlauf bei 50 bar etwa 3,4 V gemessen. Für die Messung des Raildrucks ist es oft ausreichend, den Istwert aus dem Steuergerät auszulesen. In der OBD hat man erst bei neueren Systemen Glück, dass der Systemdruckparameter angezeigt wird. Traut man dem nicht, reicht für den Anfang auch ein Multimeter, um die Spannung zu messen und die Werte mithilfe einer Tabelle in den Raildruck umzurechnen.
Bei Drehzahlschwankungen oder Fehlermeldungen, die darauf hindeuten, sollte der Diagnoseprofi ein Oszilloskop anschließen. Die Rauheit des Signales bei Motorlauf ist stark von der Art der Druckregelung und von der Mengenentnahme der Injektoren abhängig, sollte aber dazwischen nicht mehr als 400 mV betragen. Systeme mit mechanischer und hochdruckseitiger Regelung weisen eine etwas größere Rauheit als saugseitig geregelte Systeme auf.
Die abgegebene Kraftstoffmenge ist hauptsächlich von der Düsenöffnungszeit abhängig. Diese unterliegt aber auch einer durch die Druckdifferenz zwischen Brennraumdruck und Kraftstoffdruck hervorgerufenen Streuung. Von dem im Hochdruckbereich verbauten Drucksensor benötigt daher das Steuergerät immer den aktuellen Druckwert zur Berechnung der Einspritzzeit.
Speziell beim Motorstart ist das Signal des Hochdrucksensors zur Berechnung der Kraftstoffmenge von höchster Wichtigkeit. Der Druckaufbau ist in Abhängigkeit der Drehzahlschwankungen und der Temperatur des Kraftstoffs sowie der Komponenten sehr unterschiedlich und bedarf einer Kompensation durch das Steuergerät.
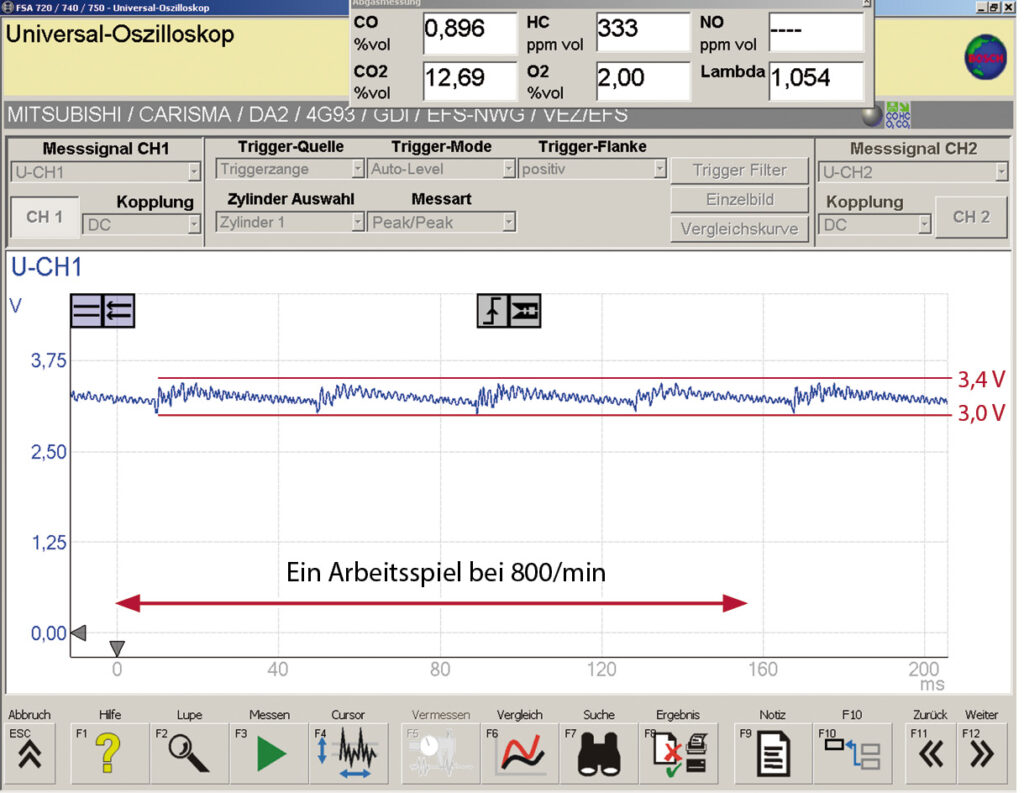
Um ein vom Kraftstoffdruck hervorgerufenes Startproblem zu erkennen, muss der Freigabedruck bekannt sein. Bei Mitsubishi GDI wird sofort eingespritzt, wenn ein verwertbares Drucksignal vom Sensor für die Startmengenberechnung vorliegt.
Ist der Sensor abgezogen oder als defekt erkannt, so kalkuliert das Steuergerät eine Temperatur und startumdrehungsabhängige Notlaufmenge.
Der Motor springt im Notlaufprogramm an. Die meisten anderen Systeme vollziehen einen Hochdruckstart, wobei erst nach dem Erreichen eines systemabhängigen Hochdruckes von 25, 40 oder 70 bar eingespritzt wird.
Das entspricht etwa dem Leerlaufdruck und damit der genannten Signalspannung. Diese ist bei entsprechenden Beanstandungen mit einem Multimeter zu prüfen, wenn kein Raildruckwert aus dem Steuergerät auszulesen ist. Steigt der Druck für eine definierte Zeit von maximal vier Sekunden über den vorgegebenen Maximaldruck, stellt das Steuergerät die Einspritzung ab und legt einen entsprechenden Fehlerspeichereintrag ab.
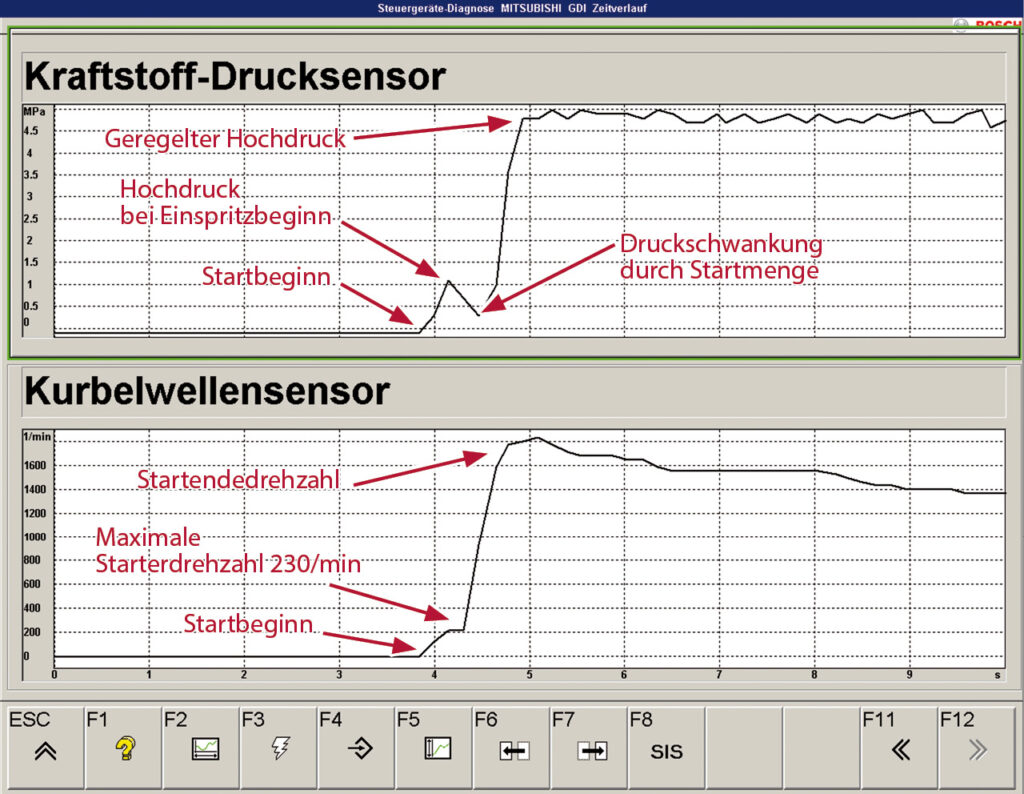
Sofern der Hochdruck bei Teillast für einige Umdrehungen und für eine definierte Zeit unter einem festgelegten Minimaldruck fällt, schaltet das Steuergerät die Einspritzung ab, bis die Drehzahl unter eine Sperrschwelle gefallen ist. Der Motor wird dann ausschließlich bis zu dieser Drehzahl und nur im Homogenmodus betrieben.
Kompliziertere Alternative
Neben den genannten Möglichkeiten ist der Hochdrucksensor nur schwer im Vergleich zu dem real anliegenden Raildruck zu prüfen. Mit einem Druckmanometer und einer entsprechenden Adaption muss der Hochdruck am Rail gemessen und gleichzeitig die Spannung oder besser noch der Druck aus dem Steuergerät ausgelesen werden.
Benzin-Direkteinspritzsysteme – Komponenten, Funktionen, Diagnose
1. Auflage 2015, von Heiko Peter, 212 Seiten, 175 Abbildungen/Grafiken/Tabellen
Ich möchte mehr Informationen zu diesem Buch!
Zum gesamten Krafthand-Fachbuchprogramm
Inhalt:
- Vergleich von Saugrohreinspritzung und Direkteinspritzung
- Kraftstoffsysteme im Überblick:
– System MELCO im Mitsubishi GDI und bei Volvo
– System Siemens der 1. Generation
– System Bosch mit HDP 1 im VW FSI-Motor (…) - Das Kraftstoff-Niederdrucksystem
- Das Kraftstoff-Hochdrucksystem
- Kraftstoffinjektoren
- Das Zündsystem
- Die Abgasnachbehandlung, Gemisch-Überwachung
Schreiben Sie den ersten Kommentar